After designing the mold, it took a while for me to plan how I was going to actually use it to make my first prototype. Without further ado, this is the resulting working model for the masturbator. Your peen goes in the scary looking cavity.
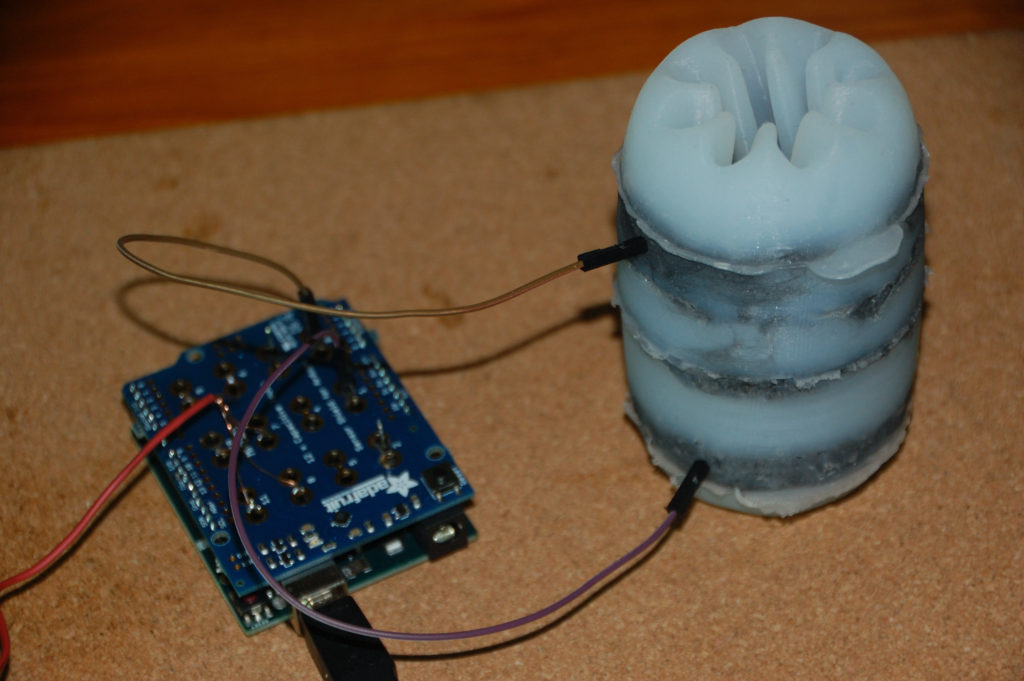
The only failure of the prototype was the silicone is too hard (shore A-10) whereas it should probably be 00-30, apart from that, it worked just as I’d hoped.
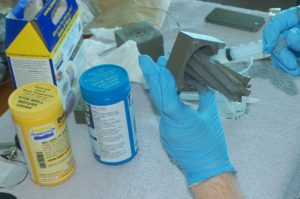
My first challenge was to get enough protective silicone around the central shaft of the negative model so that people’s privates would be protected. I started by trying to inject silicone into the ridges in the shaft. This was only partially successful.
Injecting the silicone didn’t seem to have any impact on the quality of contact between the mold and the silicone.
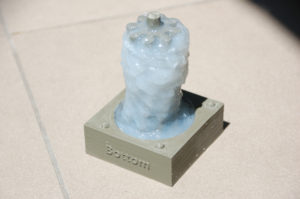
This was the one and only time that choosing a “fast cure” silicone helped me, because I was able to simply keep working the silicone around and around the central spiral with a plastic knife until it cured for me. The material became more and more “goopy” over time, but I found that even though it had a lumpy texture on the outside, the silicone was still filling in all the gaps properly.
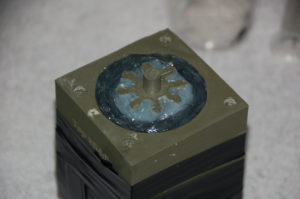
I placed the “bottom middle” piece on the bottom piece. It turns out that because ABS plastic warps a little, you have to put a fair bit of pressure on to make the pieces meet. I used insulation tape for this purpose but immediately realised that this was not the best choice. It doesn’t stick well to the ABS plastic and stretches a little.
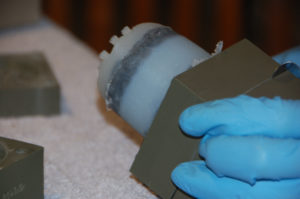
Mixing small batches of silicone is very difficult. I found that it’s easier to decant the two-part silicone into two containers beforehand and use a syringe to measure a smaller amount into a mixing container. I think that in future it would be better to have a design that allowed me to mix up larger batches of silicone.
De-molding the toy was a lot harder than I expected, probably because the silicone is harder than it should be. I am glad I made it out of four parts. Perhaps in future I should make the central shaft its own 5th part, which would make disassembling the mold much easier.
Much to my surprise, once I hooked it up to a capacitive sensor, the prototype actually works. With one electrode in the device, it can pretty much tell how far a finger is in the device.
The video below shows the device detecting a finger’s depth with just a single electrode.
With two electrodes, I can get better fidelity, though I noticed that there was interference between electrodes.
I learned the following lessons from this exercise:
- There’s a false economy to silicone, where you try to use less, but end up using more. There always seems to be left over silicone and you may be tempted to re-use it, but this may result in a worse outcome over all.
- Silicone is best additive, that is to say, it’s very hard to remove bits off silicone once it’s been cured, but it’s very easy to add bits.
- Shore A10 silicone is way too firm for the inside of a masturbator, no matter how big the cavity is, it will hurt your male bits. I think shore 00-30 would be the better bet.
- Getting silicone off a rigid mold requires deforming the silicone more than you expect.
- Super fast curing silicone is silly, especially if you are putting additives like carbon fibre in it. I think 20 / 30 minutes pot life (Medium) is what you want.
- More than two electrodes seems to be over the top since they start interfering with each other and throwing the measurements off.
As a bonus, here’s a demonstration of just how durable silicone can be:
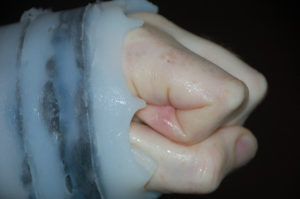